GLOSSARY
What is oil refining?
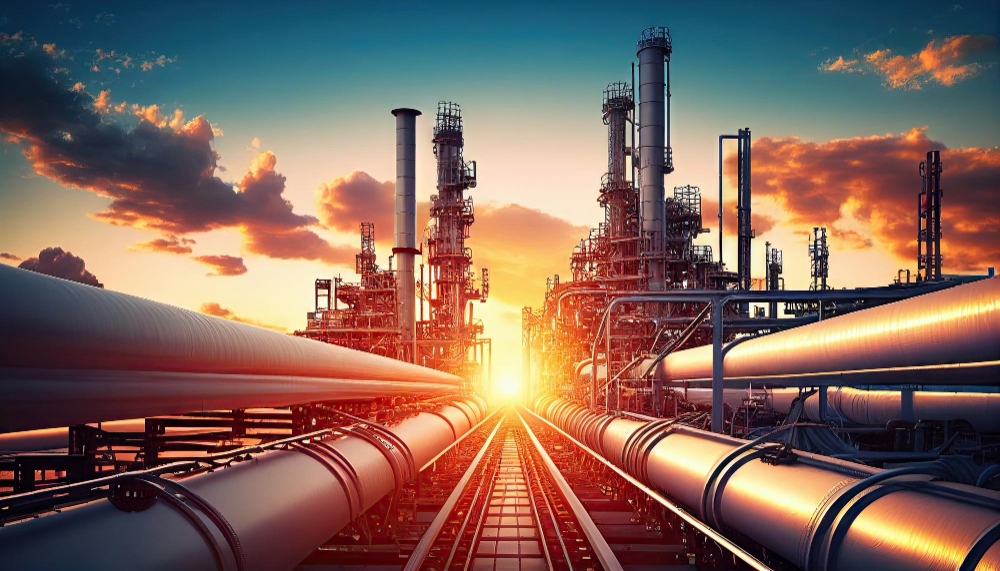
Definition and categories
Petroleum refining is an industrial process designed to convert crude oil into various finished products such as gasoline, heavy fuel oil and naphtha. As a heterogeneous mixture of various hydrocarbons, crude oil is unusable in its raw state. There are several different types of crude oil, distinguished by their viscosity and sulfur content. In order to make these components directly exploitable, it is necessary to separate them.
Generally speaking, there are two main categories of products resulting from refining:
- Energy products such as gasoline, diesel and heating oil.
- Non-energy products, such as lubricants, bitumen and naphtha used in petrochemicals.
Today's refining goes beyond the simple separation of hydrocarbons. Complex chemical processes are also involved to optimize the final products. Thus, the various petroleum cuts can undergo transformations, enhancements and blending to produce marketable goods and meet new environmental standards.
Technical or scientific operation
On arrival at the refinery, crude oil is stored in large tanks. The different varieties of crude oil are stored and separated according to their sulfur content, which is decisive in selecting the appropriate refining processes. Each refining unit houses a separate physico-chemical industrial process.
The oil refining process involves three main stages.
1) Distillation of crude oil to obtain intermediate products
Crude oil distillation comprises two complementary stages. The first, called atmospheric distillation and carried out at atmospheric pressure, separates gases, gasolines, naphtha (light cuts), kerosene and diesel (medium cuts), as well as heavy cuts. The residues from atmospheric distillation are subjected to a second distillation, known as vacuum distillation (carried out in a depressurized column), to recover additional middle products of commercial value.
-
- Atmospheric distillation involves separating the components of a liquid mixture according to their evaporation temperature. The crude oil is fed into a large distillation tower, around 60 meters high and 8 meters wide, where it is heated to around 400°C. The various hydrocarbons contained in the crude oil are vaporized successively, starting with the lightest, then the medium, and finally some of the heaviest. The temperature gradually decreases along the tower, allowing each type of hydrocarbon to liquefy for recovery. The lightest components are collected at the top of the tower, while the heaviest remain at the bottom.

Operating principle of a crude oil distillation tower
-
- Vacuum distillation is an operation designed to separate, on the same principle as atmospheric distillation, heavy products from medium product residues, by subjecting them to a second distillation phase called "vacuum distillation". A smaller column is closed and then depressurized. This pressure drop facilitates recovery of the heavy products, whose boiling temperature is lowered. Gas oil is recovered at the top of the column, and heavy fuel oil at its base. The residues from this vacuum distillation are recovered to produce lubricants.
2) Processing and improving cut quality at the various refining units
To meet the growing demand for sophisticated light products (representing 40% of total demand for refined products), the various cuts undergo various transformations and improvements at several refining units. European refineries have had to adjust to the growth in demand for diesel versus gasoline.
-
- Heavy cuts (around 40% of crude oil)
Vacuum residues undergo visbreaking. This operation, carried out in the liquid phase between 450°C and 500°C under a pressure of 5 to 20 bars, consists of thermal cracking to obtain bitumen.
Distillates are transformed by catalytic cracking at high temperature (500°C), in the presence of a catalyst that promotes chemical reactions. This treatment produces heavy fuel oils.
-
- Medium cuts (around 35% of crude oil)
Light diesel, heavy diesel and some kerosenes are upgraded by hydrodesulfurization, a hydrogen treatment designed to reduce the sulfur content of the diesel cut.
Kerosene cut from sulfur-containing crude is upgraded by hydrotreating. In the presence of the hydrogen contained in the water, hydrogen sulfide is formed, separating the sulfur from the kerosene cut and producing sweetened kerosene. Treatment with Merox, a soda-based process, renders the sulfur in low-sulfur kerosenes harmless.
-
- Light cuts (between 20% and 25% of crude oil)
Heavy gasolines are upgraded by the catalytic cracking process to produce premium automotive fuels (SP95, SP98, etc.).
To obtain these same premium fuels, light gasolines are upgraded by isomerization, to compensate for the loss of octane number due to the legal reduction in the lead content of gasolines, and by alkylation, a process which is the reverse of cracking, leading to an increase in the number of carbon atoms in an organic compound.
Naphtha is upgraded by hydrotreating to remove the sulfur. The gases it contains are then removed in a "stabilizer" and separated into two fractions. The light naphtha is stored for blending into fuels, while the heavy naphtha feeds the catalytic reforming unit. The hydrotreated naphtha cut may also be sent to a steam cracker if it is to be used for petrochemicals.
Combustible gases are directed to the refinery furnace.
Propane and butane (LPG) require no special transformation or upgrading.
3) Product manufacturing
Using dosers equipped with automatic controllers, new blends are made to obtain finished products that comply with environmental standards. To carry out this series of operations, refineries must have large storage volumes, facilities to receive raw products and dispatch finished products.
Refineries also produce lubricants to improve the operation of industrial engines and machinery, as well as ships. These oils and greases are made from the residues of vacuum distillation.

Refining transforms crude oil into numerous products with different uses.
Energy issues
Environmental issues
Refineries are responsible for the emission of pollutants and greenhouse gases. Faced with increasingly stringent regulations, refinery operators are investing in solutions to reduce these emissions, as illustrated by the example of the Esso refinery in Fos-sur-Mer, which has significantly reduced its nitrogen oxide emissions.
At the same time, these facilities use large quantities of substances that are potentially hazardous to human health and the environment. In France, their classification under the European Seveso Directive depends on the types and quantities of hazardous products they handle. This classification, established by a weighted sum of the masses of products present on the site, defines the authorized threshold. The visual and noise impacts generated by the operation of a refinery are also taken into consideration.
Financial and macroeconomic issues
The refining sector faces intermittent economic difficulties, exacerbated by an imbalance between production capacity and consumption needs, particularly strong demand. The construction of new refineries is concentrated mainly in developing countries in Asia and Africa. In addition to lower local costs than those of existing refineries, these new projects benefit from significant logistical gains to meet growing domestic demand.
-
ANALYSIS11 month ago
The 3 African countries richest in natural resources
-
FOCUS ONA1 an ago
The 10 largest oil refineries in Africa
-
NEWS8 month ago
Top 10 des pays africains producteur de l’or : Mali 2-eme, Burkina Faso 3-eme
-
NEWS2 ans ago
Ranking of oil producers: Here are the Top 10 African countries.
-
FOCUS ONA8 month ago
Top 10 oil producers in Africa in 2023
-
NEWS1 an ago
Top 20 oil producing countries in 2022
-
NEWS5 month ago
Africa's 10 largest natural gas production fields.
-
NEWS7 month ago
Ivory Coast: Eni to deploy a cylindrical FPSO and a converted FSO on the Baleine oil field